Thus far, little research has been conducted on the characterization of mechanical, electrical and chemical reliabilities of nanomaterial-based devices even if their importance cannot be ignored for real-life applications. Our group has great interests in the microscopic understanding of mechanical and chemical reliability of nanomaterial-based devices, and their improvements.
3-1. Mechanical and chemical reliability of nanomaterial-based electrodes on flexible substrate:
3-1-1.
- Mechanical strength of nanoparticle-based thin films: The mechanical properties of the solution-processed metal nanoparticle-based thin films are very important, especially for printed flexible electronic devices. We found that the solution processed metal nanoparticle-based thin films possess much smaller failure strains than those of vacuum deposited metal thin films due to granular microstructures with numerous nanoscale pores, which can easily initiate cracks under tension [52]. We are currently working on the improvement of mechanical strength of nanoparticle-based thin films by composite formation with 1D nanomaterials such as metal nanowires, which provide barrier against crack propagation [53]. On the other hand, we can also take advantage of weak mechanical property of metal nanoparticle-based thin films for stretchable strain sensors, in which the crack growth allows high strain sensitivities and reversible crack opening/closure is enabled by the elastic recovery of elastomeric substrate [54].
3-1-2.
- Surface adhesion of nanoparticle-based thin films and microstructures: Reliability of solution processed nanoparticle-based thin films for printed and flexible electronics is often limited by poor adhesion with substrates. We conducted direct measurement of the interfacial fracture energy between metal nanoparticle-based thin film and substrate by using double cantilever beam (DCB) fracture mechanics testing [55]. It was demonstrated that thermal annealing parameters affect the interfacial fracture energy, and that the interfacial fracture resistance can enhanced by bridging between organic residues from metal nanoparticles and the substrate. Furthermore, we have found that the nanostructuring of substrate surface provides high surface area as well as mechanical anchoring, thereby the adhesion strength of metal thin films is dramatically improved [56].
3-1-3.
- Low-temperature bonding of 1D nanomaterials on electrodes for flexible electronics:The adhesion strengths of common 1D nanomaterial integration processes (eg. dielectrophoresis, microcontact printing, or drop casting) rely on weak Van der Waal force. In order to provide extra adhesion strength between 1D nanomaterials and electrodes, additional processes such as focused ion beam deposition or selective electrochemical deposition are required. In order to address this issue, we developed thermocompression bonding process, in which low temperature and pressure compression of 1D nanomaterials is made directly onto metal electrodes [57, 58]. This method could provide much higher mechanical adhesion than conventional integration methods as well as parallel integration of 1D nanomaterials in large-scale substrates.
3-1-4.
- Chemical stability of nanomaterial-based electrodes on flexible substrate: Flexible electronic devices are often exposed to chemically harsh environments during their applications in wearable, biomedical and energy devices. We studied the chemical stabilities of nanomaterial-based electrodes and searched for their solutions. The first example is silver nanowire (Ag NW) based transparent electrode, which is inherently unstable to moist and chemically reactive environment. We reported remarkable stability improvement of the Ag NW network film against oxidizing and sulfurizing environment by local electrodeposition of Ni along Ag NWs, which provides the physical barrier against chemical reaction and diffusion as well as the cathodic protection from galvanic corrosion [59]. Another example is the chemical stability of metal nanoparticle thin films in salt solutions. Chlorine ions (Cl-) dissolve the organic surfactant on the metal nanoparticles and thus generate more cracks and pores within film and the interfacial adhesion on substrate is weakened. We are currently seeking for the methods to dramatically enhance the chemical resistance of metal nanoparticle thin film by various surface passivation techniques [60].
[52] S. Kim, S. Won, G-D. Sim, I. Park, and S-B. Lee, “Tensile characteristics of metal nanoparticle films on flexible polymer substrates for printed electronics applications”, Nanotechnology 24, 085701, Mar 2013
[53] S. Kim and I. Park, “Tensile characteristics of nanoparticle-nanowire composite thin films”, in preparation
[54] J. Lee, S. Kim, J. Lee, D. Yang, B.C. Park, S. Ryu and I. Park, “A stretchable strain sensor based on a metal nanoparticle thin film for human motion detection”, Nanoscale 6, 11932-11939, Aug, 2014
[55] I. Lee, S. Kim, J. Yun, I. Park, and T-S. Kim, “Interfacial toughening of solution processed Ag nanoparticle thin films by organic residuals”, Nanotechnology 23, 485704, Dec 2012
[56] H. Eom, J-H. Kim, J. Hur, T-S. Kim, S-K. Sung, J-H. Choi, E. Lee, J-H. Jeong, and I. Park, “Nanotextured polymer substrate for flexible and mechanically robust metal electrodes by nanoimprint lithography”, ACS Applied Materials & Interfaces 7, 45, 25171-25179, Oct 2015
[57] W.S. Lee, J-H. Choi, I. Park*, and J.H. Lee, “Room-temperature compressive transfer printing of nanowires for nanoelectronic devices”, Langmuir 28, 17851, Dec 2012 (* co-corresponding authors)
[58] W.S. Lee, S. Won, J. Park, J. Lee, and I. Park, “Thermo-compressive transfer printing for facile alignment and robust device integration of nanowires”, Nanoscale 4, 3444-3449, Mar 2012
[59] H. Eom, J. Lee, A. Pichitpajongkit, M. Amjadi, J-H. Jeong, E. Lee, J-Y. Lee and I. Park,”Ag@Ni core-shell nanowire network for robust transparent electrodes against oxidation and sulfurization”, Small 10, 4171, Jun 2014
[60] S. Kim and I. Park, “Chemical resistance of metal nanoparticle thin films in ionic liquid environment”, in preparation
[53] S. Kim and I. Park, “Tensile characteristics of nanoparticle-nanowire composite thin films”, in preparation
[54] J. Lee, S. Kim, J. Lee, D. Yang, B.C. Park, S. Ryu and I. Park, “A stretchable strain sensor based on a metal nanoparticle thin film for human motion detection”, Nanoscale 6, 11932-11939, Aug, 2014
[55] I. Lee, S. Kim, J. Yun, I. Park, and T-S. Kim, “Interfacial toughening of solution processed Ag nanoparticle thin films by organic residuals”, Nanotechnology 23, 485704, Dec 2012
[56] H. Eom, J-H. Kim, J. Hur, T-S. Kim, S-K. Sung, J-H. Choi, E. Lee, J-H. Jeong, and I. Park, “Nanotextured polymer substrate for flexible and mechanically robust metal electrodes by nanoimprint lithography”, ACS Applied Materials & Interfaces 7, 45, 25171-25179, Oct 2015
[57] W.S. Lee, J-H. Choi, I. Park*, and J.H. Lee, “Room-temperature compressive transfer printing of nanowires for nanoelectronic devices”, Langmuir 28, 17851, Dec 2012 (* co-corresponding authors)
[58] W.S. Lee, S. Won, J. Park, J. Lee, and I. Park, “Thermo-compressive transfer printing for facile alignment and robust device integration of nanowires”, Nanoscale 4, 3444-3449, Mar 2012
[59] H. Eom, J. Lee, A. Pichitpajongkit, M. Amjadi, J-H. Jeong, E. Lee, J-Y. Lee and I. Park,”Ag@Ni core-shell nanowire network for robust transparent electrodes against oxidation and sulfurization”, Small 10, 4171, Jun 2014
[60] S. Kim and I. Park, “Chemical resistance of metal nanoparticle thin films in ionic liquid environment”, in preparation
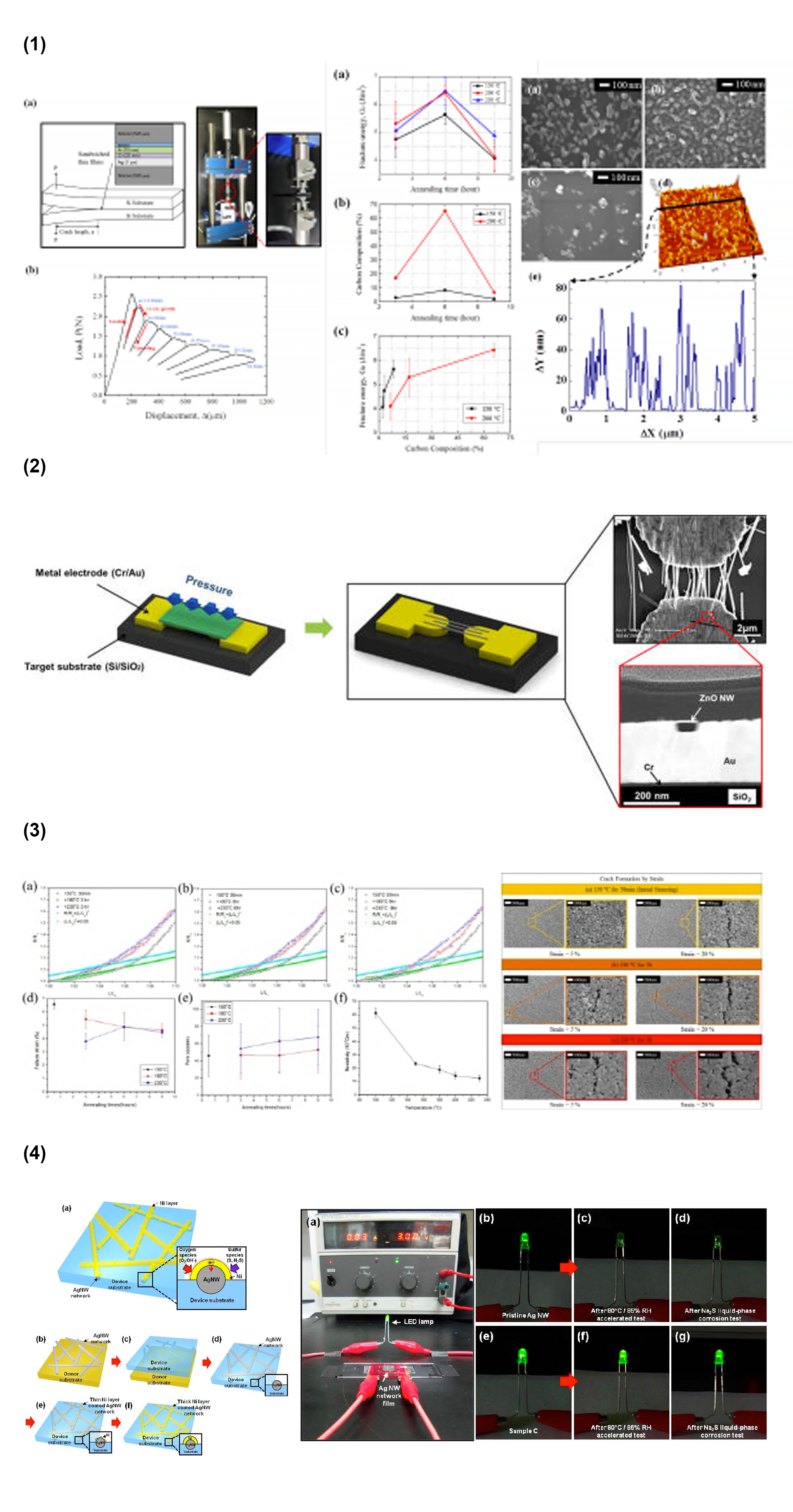
Figure 6. Mechanical and chemical reliability of nanomaterial-based devices: (1) tensile characteristics of metal nanoparticle-based thin film (I. Park, et al., Nanotechnology 2013), (2) low-temperature, low-pressure compressive bonding of nanowires on metal electrodes (I. Park, et al., Langmuir 2012), (3) adhesion characteristics of metal nanoparticle-based thin film (I. Park, et al., Nanotechnology 2012), and (4) Ni-AgNW core-shell nanostructures for chemically resistant transparent conductor film (I. Park, et al., Small 2014)