Nanomaterials exhibit distinct physical and chemical properties, enabling their applications to physical and chemical sensors with high performances, low-power consumption and high density device integration. Our group is working on the design and fabrication of chemical (eg. gas molecules and ions) and physical (eg. strain, force, pressure and light) sensors based on functional nanoparticles, nanowires, nanotubes, and their hybrid nanocomposites.
1-1. Physical sensors based on functional micro/nano-structures:
1-1-1.
- Flexible and stretchable strain sensors by elastomer-nanomaterial composite: The demand for flexible and wearable electronic devices is rapidly increasing. Especially, highly stretchable and flexible strain sensors are very useful for the human motion detection towards healthcare applications [1]. We have developed highly flexible, stretchable, and sensitive strain sensors based on the nanocomposite of elastomeric polymers and one dimensional (1D) nanomaterials (eg. silver nanowires and carbon nanotubes) [2, 3]. These types of sensors provide high piezoresistivity and stretchability due to the percolation network of 1D nanomaterials and elastic properties of elastomeric matrix, respectively. Another type of stretchable strain sensor utilizes the reversible crack opening/closure of metal nanoparticle thin film [4]. The optimization of sensing performances of stretchable strain sensors has also been made using numerical simulation [5]. Furthermore, we also have developed 3D strain sensor using the conductive nanocomposite and electrical impedance tomography for multi-touch, 3D sensing [6].
1-1-2.
- Soft and highly sensitive force sensors by microporous elastomers and their composites with conductive nanomaterials: Recently, wearable and flexible force / pressure sensors become very promising in their potential applications in electronic skin, touch-based display, and soft robotics. We have developed highly sensitive and ultra-soft force sensors by using microporous elastomers as dielectric layers in the capacitive sensors [7] and microporous elastomer-conductive 1D nanomaterial composites as piezoresistive layers in the resistive sensors [8]. These multiscale approaches allow ultra-low detection limit, high sensitivity as well as wide working range of force detection. We believe that these sensors would be very useful for wearable human-machine interface as well as for healthcare applications.
[1] M. Amjadi, K-U. Kyung, I. Park, and M. Sitti, “Stretchable, skin-mountable, and wearable strain sensors and their potential applications: A review”, Advanced Functional Materials 26, 1678-1698, Mar 2016
[2] M. Amjadi, A. Pichitpajongkit, S. Lee, S. Ryu and I. Park, “Highly stretchable and sensitive strain sensor based on silver nanowire-elastomer nanocomposite”, ACS Nano 8, 5154-5163, Apr 2014
[3] M. Amjadi, Y. Yoon and I. Park, “Ultra-stretchable and skin-mountable strain sensors using CNTs-Ecoflex nanocomposite”, Nanotechnology 26, 375501, Aug 2015
[4] J. Lee, S. Kim, J. Lee, D. Yang, B.C. Park, S. Ryu and I. Park, “A stretchable strain sensor based on a metal nanoparticle thin film for human motion detection”, Nanoscale 6, 11932-11939, Aug 2014
[5] S. Lee, M. Amjadi, N. M. Pugno, I. Park, and S. Ryu,”Computational analysis of silver nanowires-elastomer nanocomposite based strain sensors”, AIP Advances 5, 117233, Nov 2015
[6] H. Lee, D. Kwon, J. Cho, I. Park, and J. Kim, “Soft nanocomposite based multi-point, multi-directional strain mapping sensor using anisotropic electrical impedance tomography”, Scientific Reports 7, 39837, Jan 2017
[7] D. Kwon, T. Lee, M. S. Kim, S. Kim, T.-S. Kim and I. Park, “Highly Sensitive, Flexible and Wearable Pressure Sensor Based on a Giant Piezocapacitive Effect of Three-Dimensional Microporous Elastomeric Dielectric Layer”, ACS Applied Materials & Interfaces 8, 16922-16931, Jun 2016
[8] M. Amjadi, M. S. Kim and I. Park, “Flexible and sensitive foot pad for sole distributed force detection”, Proceedings of 14th International Conference on Nanotechnology (IEEE-NANO 2014), 764-767, Aug 2014
[2] M. Amjadi, A. Pichitpajongkit, S. Lee, S. Ryu and I. Park, “Highly stretchable and sensitive strain sensor based on silver nanowire-elastomer nanocomposite”, ACS Nano 8, 5154-5163, Apr 2014
[3] M. Amjadi, Y. Yoon and I. Park, “Ultra-stretchable and skin-mountable strain sensors using CNTs-Ecoflex nanocomposite”, Nanotechnology 26, 375501, Aug 2015
[4] J. Lee, S. Kim, J. Lee, D. Yang, B.C. Park, S. Ryu and I. Park, “A stretchable strain sensor based on a metal nanoparticle thin film for human motion detection”, Nanoscale 6, 11932-11939, Aug 2014
[5] S. Lee, M. Amjadi, N. M. Pugno, I. Park, and S. Ryu,”Computational analysis of silver nanowires-elastomer nanocomposite based strain sensors”, AIP Advances 5, 117233, Nov 2015
[6] H. Lee, D. Kwon, J. Cho, I. Park, and J. Kim, “Soft nanocomposite based multi-point, multi-directional strain mapping sensor using anisotropic electrical impedance tomography”, Scientific Reports 7, 39837, Jan 2017
[7] D. Kwon, T. Lee, M. S. Kim, S. Kim, T.-S. Kim and I. Park, “Highly Sensitive, Flexible and Wearable Pressure Sensor Based on a Giant Piezocapacitive Effect of Three-Dimensional Microporous Elastomeric Dielectric Layer”, ACS Applied Materials & Interfaces 8, 16922-16931, Jun 2016
[8] M. Amjadi, M. S. Kim and I. Park, “Flexible and sensitive foot pad for sole distributed force detection”, Proceedings of 14th International Conference on Nanotechnology (IEEE-NANO 2014), 764-767, Aug 2014
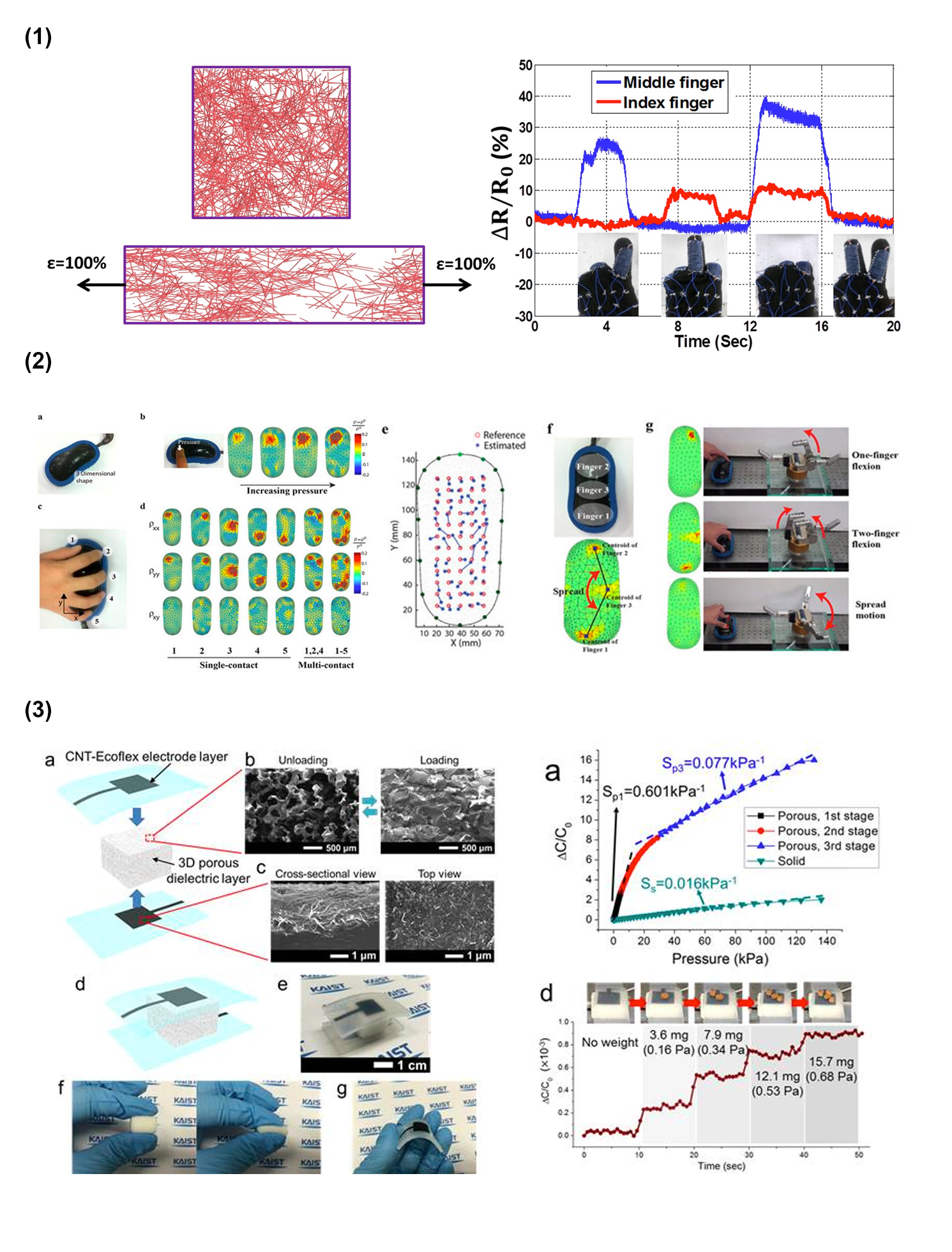
Figure 1. Flexible and stretchable physical sensors based on functional micro/nano-structures: (1) silver nanowire-PDMS composite based stretchable strain sensor (I. Park, et al., ACS Nano 2014), (2) 3D strain mapping sensor using conductive nanocomposite and electrical impedance tomography method (I. Park, J. Kim, et al., Scientific Reports, 2017), and (3) soft and sensitive pressure sensor using microporous elastomer (I. Park, et al., ACS Appl. Mater. Inter. 2016)